سولفات آمونیوم چیست؟
سولفات آمونیوم ([NH4]2SO4) عموما به عنوان کود کشاورزی مورد استفاده قرار میگیرد و یکی از اولین کودهای نیتروژندار در صنایع کشاورزی است که کاربرد وسیعی پیدا کرده است.
بیش از 75 درصد سولفات آمونیوم تولیدی در دنیا به عنوان کود کشاورزی مورد استفاده قرار میگیرد.
حلالیت بالای این کود یکی از ویژگیهای آن است که استفاده از این ماده را در کشاورزی تسهیل کرده است.
مفاهیمی که در این مقاله به آنها پرداختیم،عبارتند از:
سولفات آمونیوم چیست و چرا یکی از کودهای پرکاربرد دنیاست؟
بازار کود سولفات آمونیوم
فناوری و روش تولید سولفات آمونیوم
مسائل و چالشهای زیستمحیطی
سولفات آمونیوم چیست و چرا یکی از کودهای پرکاربرد دنیاست؟
خواص فیزیکی مطلوب، پایداری شیمیایی و اثرگذاری سولفات آمونیوم در رشد گیاهان از جمله ویژگیهای این ماده است.
جدول زیر مهمترین خواص فیزیکی و شیمیایی سولفات آمونیوم را نشان میدهد.
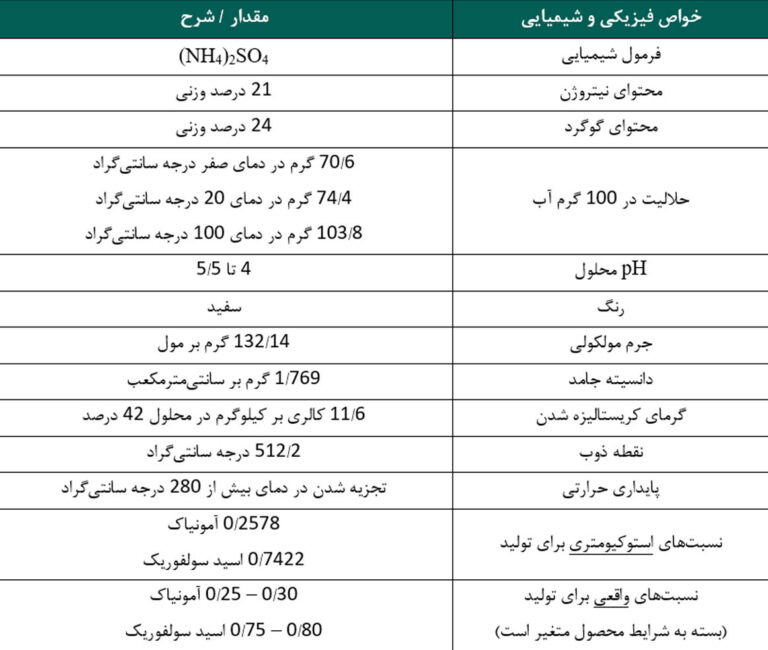
سولفات آمونیوم تجاری از نظر رنگ عموما سفید است اما رنگ آن میتواند از سفید تا زرد و خاکستری نیز تغییر یابد.
تغییر رنگ سولفات آمونیوم به دلیل وجود برخی ناخالصیها در ترکیب آن است. سولفات آمونیومی که به عنوان محصول جانبی فرایندهای مختلف بدست میآید، اسید آزاد ندارد.
گریدهای دیگری از این محصول میتوانند تا 15/0 درصد نیز اسید آزاد (سولفوریک اسید) داشته باشند اما به طور کلی میزان اسید آزاد نباید بیش از 03/0 درصد وزنی باشد.
وجود مقادیر بیشتر اسید آزاد در این محصول ممکن است موجب ایجاد کلوخه یا کیک سخت در فرایندهای حمل و نقل شود.این مساله بعضا با خنثی کردن اسید آزاد توسط آمونیاک کنترل میشود.
سولفات آمونیوم با توجه به فرآیند تولید در دو نوع گرانول و کریستال به بازار عرضه میشود.
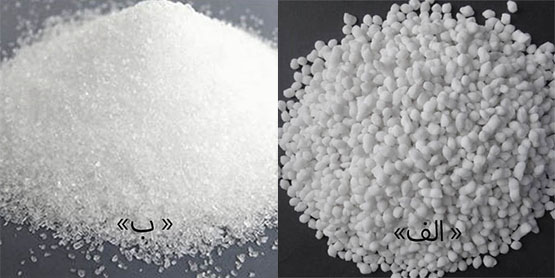
سولفات آمونیوم (الف) کریستالی و (ب) گرانول
کاربرد سولفات آمونیوم عموما در مواردی است که نیاز به مکملهای حاوی نیتروژن و گوگرد وجود دارد.
این ترکیبات، موجب تامین مواد مورد نیاز برای رشد گیاهان میشوند.
سولفات آمونیوم منبع بسیار غنی از گوگرد برای تامین مواد مورد نیاز رشد بسیاری از محصولات کشاورزی است اما به دلیل داشتن 21 درصد نیتروژن، ممکن است کودهای دیگری در کنار آن نیز استفاده شوند.
به دلیل وجود عامل نیتروژندار در ترکیب سولفات آمونیوم، این ماده برای خاکهای فرسایش دیده و سیلزده برای تولید برنج، باغها و گلخانهها کاربرد وسیعی دارد.
محلول حاوی سولفات آمونیوم حل شده معمولا به اسپریهای علفکش اضافه میشود تا اثرگذاری این مواد را افزایش دهد.
پس از اضافه کردن سولفات آمونیوم به خاک، سولفات آمونیوم به اجزای خود حل میشود.
در صورتی که این ماده در سطح خاک باقی بماند، آمونیاک مستعد اتلاف گاز در شرایط قلیایی است.
در این شرایط، وارد کردن محلول به داخل خاک و یا استفاده از آن قبل از آبیاری یا بارندگی احتمالی لازم است.
بسیاری از محصولات کشاورزی امکان استفاده از هر دو شکل امونیاک و نیتراتِ نیتروژن را برای رشد دارند.
در خاکهای گرم میکروبها سریعا اقدام به تبدیل کردن آمونیاک به نیترات میکنند. در طول این واکنش میکروبی، یون H+ آزاد میشود و اسیدیته خاک بالا میرود.
سولفات آمونیوم تاثیر اسیدی کردن بر خاک دارد و عمده این تاثیر به دلیل فرایند نیتراته شدن است و ارتباطی به وجود سولفات ندارد زیرا سولفات تنها به اندازه ناچیزی بر روی pH اثرگذار است.
از جمله سایر کاربردهای سولفات آمونیوم میتوان به افزودن آن به نان به عنوان نرم کننده خمیر اشاره کرد.
همچنین از این ماده به عنوان یکی از اجزای مواد ضد حریق در کپسولهای آتشنشانی استفاده میشود. همچنین کاربردهای دیگری در صنایع شیمیایی، چوب، کاغذ و دارویی دارد.
شکل زیر، سهم بازار هر یک از کاربردهای مختلف سولفات آمونیوم را نشان میدهد.
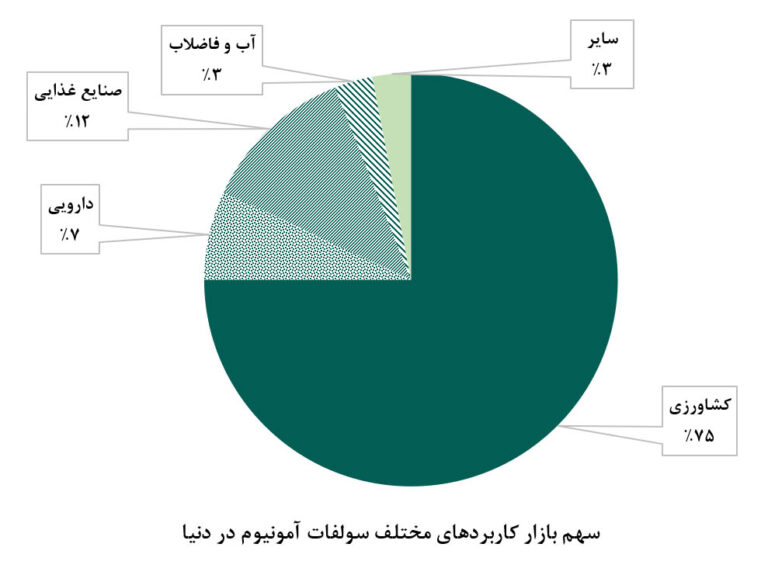
سولفات آمونیوم مانند سایر مواد کودی آمونیاکی ماهیتا اسیدی است و بر اساس مطالعات انجام شده زمانی که به خاک افزوده میشود، افزایشی در غلظت یون هیدروژن محلول موجود در خاک اتفاق میافتد.
زمانی که اسیدی بودن خاک افزایش مییابد، بسیاری از فرایندهای مفید در خاک شروع میشوند.
اسیدی شدن خاک در اثر افزودن سولفات آمونیوم میتواند با استفاده از آهک یا سایر مواد قلیایی کنترل شود.
مطالعات نشان داده است که استفاده پیوسته از سولفات آمونیوم بدون اضافه کردن آهک منجر به تولید موادی در خاک میشود که برای گیاهان سمی هستند.
در صورتی که سولفات آمونیوم در محیطهای مرطوب به خاک اضافه شود، اسید آزاد تولید میشود و با ترکیبات کلسیم و منیزیمدار موجود در خاک واکنش میدهد.
در صورت عدم وجود این ترکیبات، اسید تولید شده با ترکیبات آهن، آلومینیم و منگنزدار واکنش میدهد که ممکن است موجب ایجاد ترکیبات سمی در طولانی مدت شوند.
در صورتی که خنثی کردن حالت اسیدی خاک در اثر اضافه کردن سولفات آمونیوم به صورت کارامد انجام شود، ترکیبات سمی ایجاد نخواهد شد.
همچنین در صورتی که سولفات آمونیوم با کودهای کلردار ترکیب شود نیز ممکن است ترکیبات سمی در خاک ایجاد کند.
نمودار زیر وضعیت تقاضای جهانی برای سولفات آمونیوم را به تفکیک کاربردهای آن نشان میدهد.
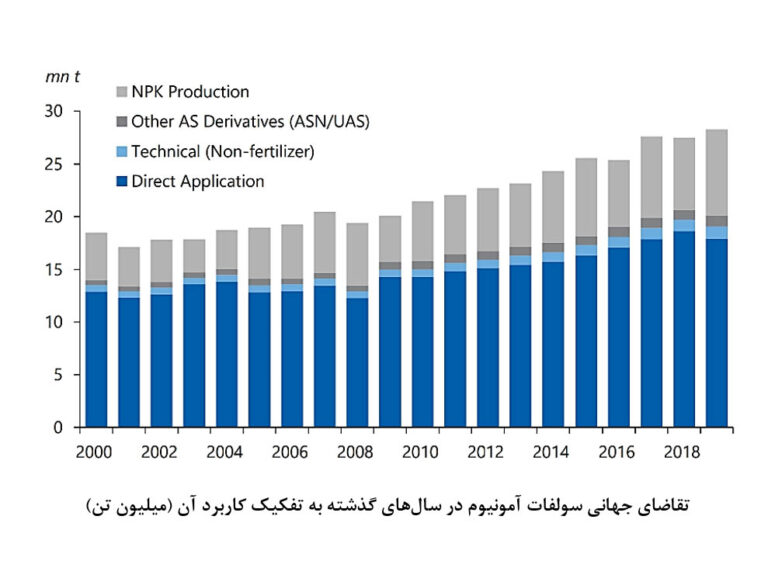
کد آیسیک سولفات آمونیوم 2412612327 و کد تعرفه گمرکی آن 31022100 است.
استاندارد ملی ایران به شماره 76 (تجدیدنظر در سال 1394) نیز به ویژگیها و روشهای آزمون کود آمونیوم سولفات پرداخته است.
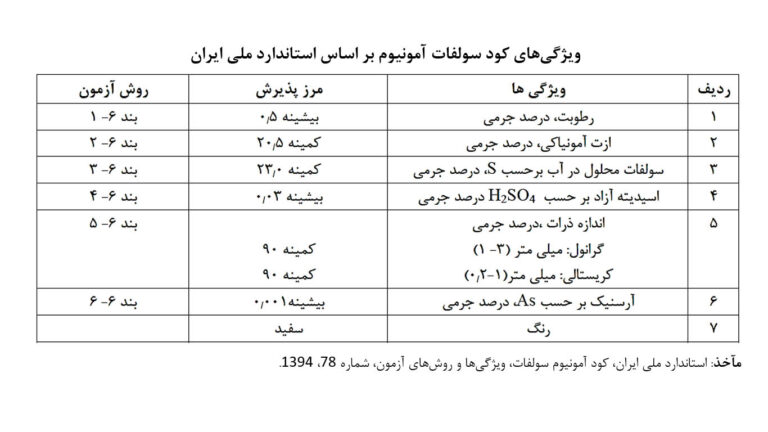
بازار کود سولفات آمونیوم
عرضه محصول سولفات آمونیوم در داخل کشور به دو طریق فروش در بازار آزاد و توزیع توسط سازمان خدمات حمایتی کشاورزی (به صورت یارانهای) انجام میشود.
عرضه این محصول در سالهای اخیر صرفا توسط شرکت پتروشیمی ارومیه و تا مرداد ماه 1399 در بورس کالا انجام شده است.
آخرین قیمت معامله شده سولفات آمونیوم در بورس کالای ایران در مردادماه 1399 به میزان 16.500 ریال بر کیلوگرم بوده است.
در حال حاضر (بهار 1402) معامله هر تن سولفات آمونیوم گرانول در بازار آزاد داخلی به قیمت 220 – 200 دلار انجام میشود.
همچنین شرکت خدمات حمایتی کشاورزی بر اساس نرخنامه فروش اعلامی برای سال 1401، سولفات آمونیوم را به قیمت هر کیلوگرم 50.000 ریال به صورت یارانهای به کشاورزان عرضه کرده است.
قیمت سولفات آمونیوم ایران عموما متناسب با قیمت سولفات آمونیوم گرانول چینی (بعلاوه هزینههای حمل از چین تا ایران) است.
شکل زیر تغییرات قیمت انواع سولفات آمونیوم را در دنیا در سالهای 2021 و 2022 نشان داده است.
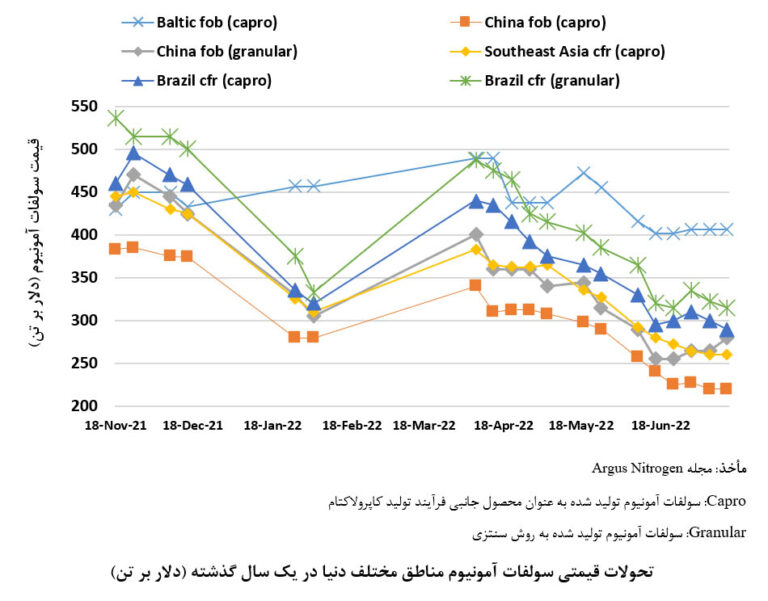
جدول زیر نیز قیمت فروش محصول سولفات آمونیوم کریستال (کریستال ریز) تولیدی شرکت پتروشیمی ارومیه را در سالهای اخیر نشان داده است.
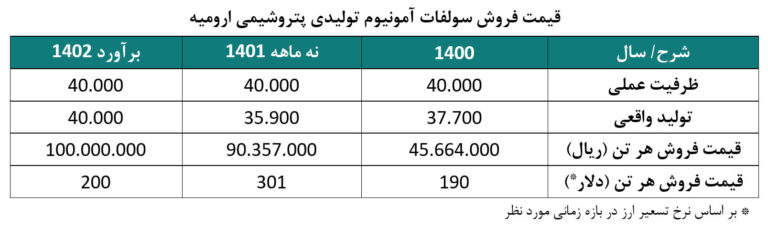
مهمترین محصول رقیب کود سولفات آمونیوم، اوره است.
اوره و سولفات آمونیوم هر دو جزو کودهای نیتروژندار محسوب میشوند با این تفاوت که اوره دارای 45 درصد نیتروژن و سولفات آمونیوم دارای 21 درصد نیتروژن است.
سولفات آمونیوم در کنار نیتروژن دارای حدود 23 درصد گوگرد نیز میباشد همچنین کود سولفات آمونیوم دارای pH پایینتری نسبت به اوره است که مناسب خاکهای کشاورزی قلیایی است.
کاربرد کودهای کشاورزی نیتروژندار همان طور که در بخش سوم این طرح اشاره شده است،در دنیا به صورت ترکیبی بوده اما در ایران به دلیل میزان تولید بالای اوره و همچنین یارانهای بودن آن مصرف اوره بیش از حد معمول و استاندارد بوده است.
با توجه به ضرورت افزایش راندمان صنعت کشاورزی و همچنین کمبود منابع آب،چارهای جز استفاده از کودهای ترکیبی وجود ندارد و همین امر موجب رشد مصرف کودهای نیتروژندار (به جز اوره) در سالهای آینده خواهد شد.
ظرفیتهای ایجاد شده در کشور برای تولید سولفات آمونیوم با توجه به آخرین آمار سال 1400، حدود 400 هزار تن در سال است.
جدول زیر، مهمترین شرکتهای فعال در زمینه تولید سولفات آمونیوم را نشان میدهد.
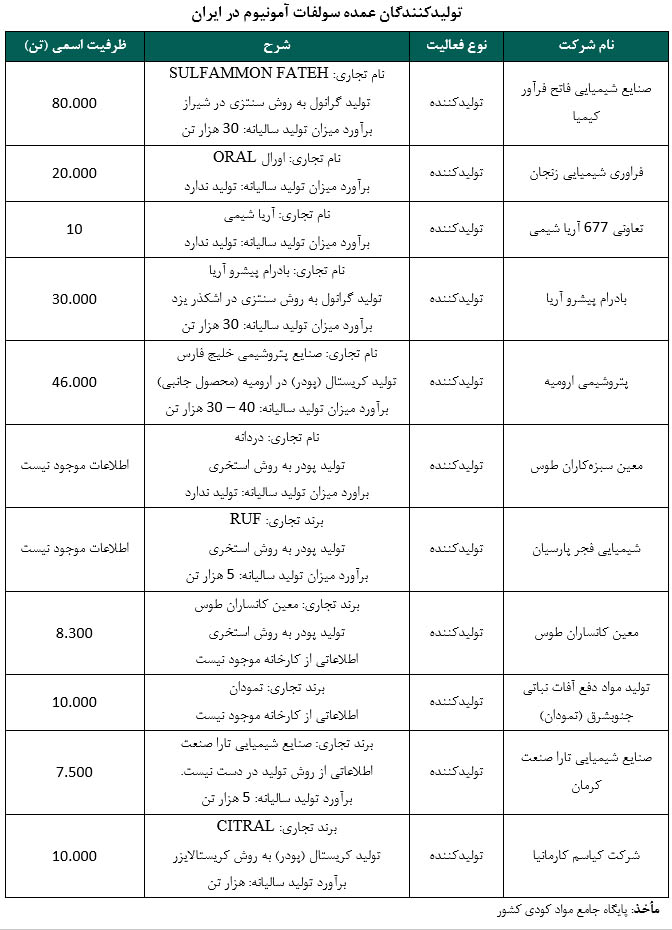
بر اساس مطالعات میدانی انجام شده، شرکت کیمیا پژوهان خاور شیمی در استان گلستان نیز یکی دیگر از واحدهای تولیدکننده سولفات آمونیوم کشور است که ظرفیتی نزدیک به 20 هزار تن در سال دارد.
همچنین طرحهای دیگری در حال راهاندازی در استانهای کرمان و فارس در مجموع به ظرفیت 260 هزار تن وجود دارند.
بنابراین میتوان گفت کل ظرفیت تولید انواع سولفات آمونیوم کریستالی و گرانوله در کشور بیش از 400 هزار تن است.
سایر شرکتهای فعال در زمینه تامین سولفات آمونیوم در کشور که از وزارت جهاد کشاورزی کد کودی دریافت کردهاند و لیست آنها در سامانه جامع مواد کودی کشور وجود دارد، شرکتهای توزیعکننده یا واردکننده این محصول هستند.
براساس بررسیهای انجام شده در حال حاضر حداکثر میزان تولید سولفات آمونیوم در کشور 100 هزار تن در سال است که بیش از 80 درصد از تولید توسط سه شرکت بادرام پیشرو آریا (تولیدکننده سولفات آمونیوم گرانول در اشکذر یزد)،
پتروشیمی ارومیه (تولیدکننده سولفات آمونیوم پودری (شبه کریستال) در ارومیه) و فاتح فرآور کیمیا (تولیدکننده سولفات آمونیوم گرانول در فارس) انجام میشود.
شرکت سهامی ذوب آهن اصفهان نیز محصول سولفات آمونیوم را به عنوان محصول جانبی فرآیند ککسازی تولید میکند که به دلیل عدم استاندارد بودن محصول، کد کودی دریافت نکرده است اما محصول آن در بازار به فروش میرسد.
برآورد میشود سالیانه 10 تا 15 هزار تن کود سولفات آمونیوم توسط واحد سولفات آمونیوم شرکت سهامی ذوب آهن اصفهان تولید میشود.
جدول زیر، میزان (تناژ) و ارزش واردات محصول را در سالهای 1396 تا 1401 نشان میدهد.
کد آیسیک سولفات آمونیوم 2412612327 و کد تعرفه گمرکی آن 31022100 است.
میزان واردات سولفات آمونیوم به کشور در سالهای اخیر به طور متوسط سالیانه 20.200 تن و متوسط ارزش واردات این محصول هر تن 230 دلار بوده است.
عمده واردات سولفات آمونیوم از کشورهای ازبکستان، امارات متحده عربی، کرهجنوبی، چین، هند، ایتالیا و سوئیس انجام شده است.
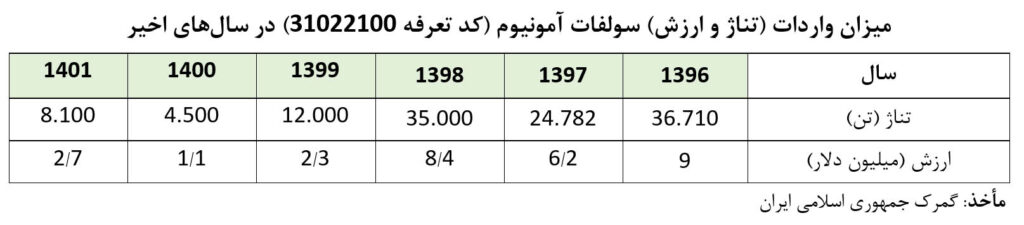
کد تعرفههای گمرکی 31022900 مربوط به املاح مضاعف و مخلوطهاي سولفات آمونيوم و نيترات آمونيوم است که میزان واردات آن قابل توجه نیست.
در دهههای گذشته به دلیل فقدان زیرساختهای تولید داخلی سولفات آمونیوم (هم از منظر تکنولوژی و هم از منظر تامین مواد اولیه) و واردات سولفات آمونیوم از کشور ازبکستان (Maxam Chirchiq) که در بازار به کریستال ازبک معروف بوده است، این محصول وارداتی توانست تا محصول غالب مورد تقاضای بازار داخلی شود و حتی استاندارد ملی ایران برای کود سولفات آمونیوم بر مبنای مشخصات فیزیکی و شیمیایی این محصول تدوین گردد.
این در حالی است که خاکهای کشاورزی ایران عمدتا قلیایی بوده و نیازمند استفاده از کودهای شیمیایی با pH پایینتر از کود کریستال ازبک است و کشاورزان مجبور بودند در کنار کودهای نیتروژندار مورد استفاده مانند اوره و سولفات آمونیوم، از محلول اسید سولفوریک برای تنظیم pH خاک استفاده کنند.
در کنار کود سولفات آمونیوم کریستال وارداتی از ازبکستان، تولیدکنندگان سولفات آمونیوم کریستالی در کشور شرکتهای پتروشیمی ارومیه (ظرفیت اسمی 46 هزار تن در سال) و ذوب آهن اصفهان (ظرفیت اسمی 15 هزار تن در سال) هستند که تقاضای داخلی برای محصول پتروشیمی ارومیه به دلیل ریز بودن سایز محصول نسبت به نمونه وارداتی ازبک کمتر بوده و محصول تولیدی ذوب آهن اصفهان به دلیل نداشتن استانداردهای لازم، کد کودی از جهاد کشاورزی دریافت نکرده است (اما همچنان در بازار و با قیمتهای پایین به فروش میرسد).
در رابطه با هر دو تولیدکنندهی داخلی مذکور، به دلیل اینکه محصول تولیدی این واحدها به نوعی محصول جانبی این واحدهای صنعتی محسوب میشود، دارای قیمت تمام شدهی پایینتری نسبت به سولفات آمونیوم تولیدی در سایر واحدهای موجود در کشور هستند.
با فراهم شدن امکان تامین اسید سولفوریک ارزان قیمت و به میزان کافی (اسید تولیدی در مجتمعهای شرکت ملی صنایع مس ایران) و همچنین رشد ظرفیت تولید آمونیاک در کشور و توسعه تکنولوژی تولید سولفات آمونیوم گرانول، تولیدکنندگان داخلی توانستند تا کود سولفات آمونیوم گرانول مورد نیاز کشور را تولید کنند.
این مساله در کنار وجود چالشهای ارزی برای واردات، موجب کاهشی شدن روند واردات سولفات آمونیوم ازبک به کشور شده است به طوری که برای اولین بار، در سال 1400 به میزان 15.700 تن سولفات آمونیوم تولیدی در ایران به کشورهای ترکیه، عراق و افغانستان صادر شد.
میزان واردات سولفات آمونیوم در سال 1400 نیز کاهش قابل توجهی داشت و به 4.543 تن رسید.
این در حالی است که در سالهای 1396، 1397 و 1398 به ترتیب واردات سولفات آمونیوم به کشور 36.700 تن، 24.700 تن و 35.000 تن بوده است. واردات سولفات آمونیوم از سال 1399 و به دلایل ذکر شده در فوق کاهش یافت و به 12.000 تن رسید که این میزان در سال 1400 به کمتر از 4.600 تن رسیده است.
روندهای جهانی نیز نشان میدهد که تقاضای دو گرید گرانول کروی شکل و کریستال درشت سولفات آمونیوم نسبت به سایر انواع این کود بیشتر است و گرانول کروی شکل رتبه نخست تقاضا را در جهان به خود اختصاص داده است.
شکل زیر این مساله را نشان داده است و شکل بعدی تحولات واردات سولفات آمونیوم کشور برزیل را بر اساس شکل محصول نشان میدهد.
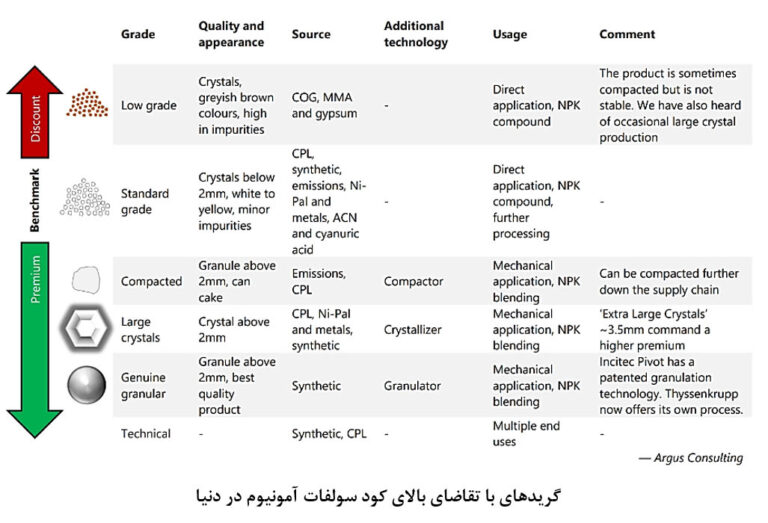
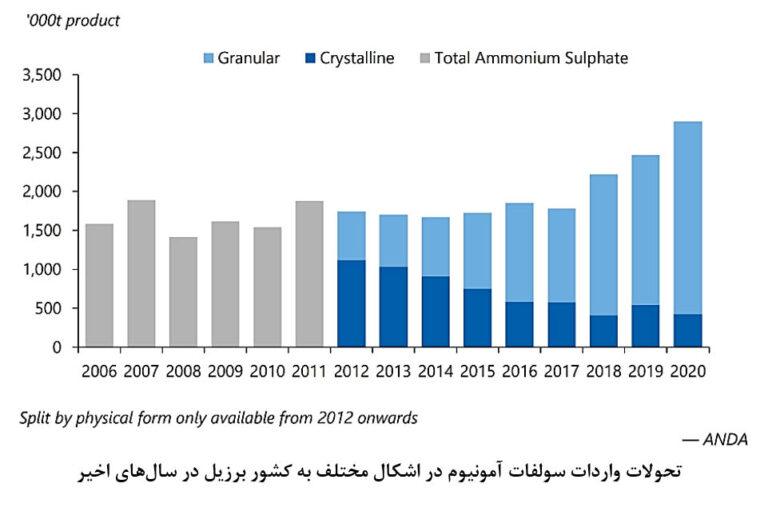
برآورد میزان مصرف ظاهری کود سولفات آمونیوم از طریق آمارهای رسمی نشان میدهد سالیانه حدود 120 تا 150 هزار تن مصرف ظاهری این کود بوده است.
آمارهای موجود در فهرست مناقصات برگزار شده برای خرید کود سولفات آمونیوم در وبسایت شرکت خدمات حمایتی کشاورزی نیز نشان میدهد از کل میزان مصرف داخلی کود سولفات آمونیوم، حدود 30 درصد از طریق مناقصههای برگزار شده توسط شرکت مذکور بوده است و مابقی در بازار آزاد به فروش رسیده که آمار و اطلاعات دقیقی از آن در دسترس نیست.
همچنین برآورد تقاضای داخلی این محصول از اطلاعات و دادههای موجود در معاملات بورس کالای ایران امکانپذیر نیست زیرا عرضه این محصول در بورس کالا (که آخرین بار در بهار 1399 انجام شده است) صرفا با هدف کشف قیمت کالا بوده است.
صادرات کود سولفات آمونیوم در سالهای گذشته نزدیک به صفر بوده اما از سال 1400 مجوز صادرات این محصول توسط وزارت جهاد کشاورزی صادر شده است.
عمده صادرات این محصول به ترکیه، افغانستان، اوکراین، عراق و سوریه است.
در حال حاضر بعضا در دورههای زمانی خاص صادرات این محصول به دلیل نیاز داخل، محدود میشود.
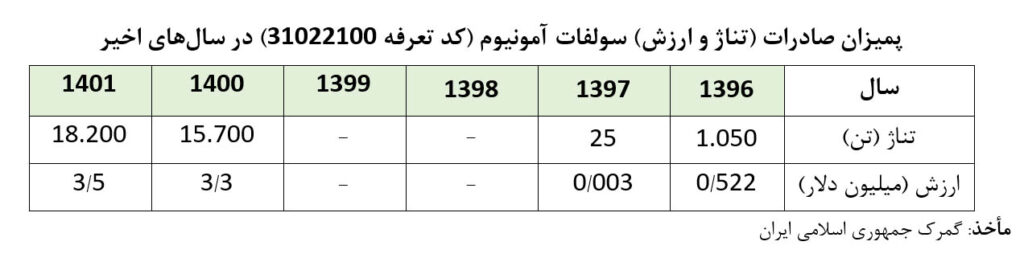
در سال 1401 میزان واردات سولفات آمونیوم کمتر از 9 هزار تن و میزان صادرات آن به بیش از 18 هزار تن بوده است.
میزان صادرات محصول در سالهای قبل از 1400 قابل توجه نبوده و با توجه به نیاز داخلی محدودیتهایی برای صادرات آن در نظر گرفته شده است.
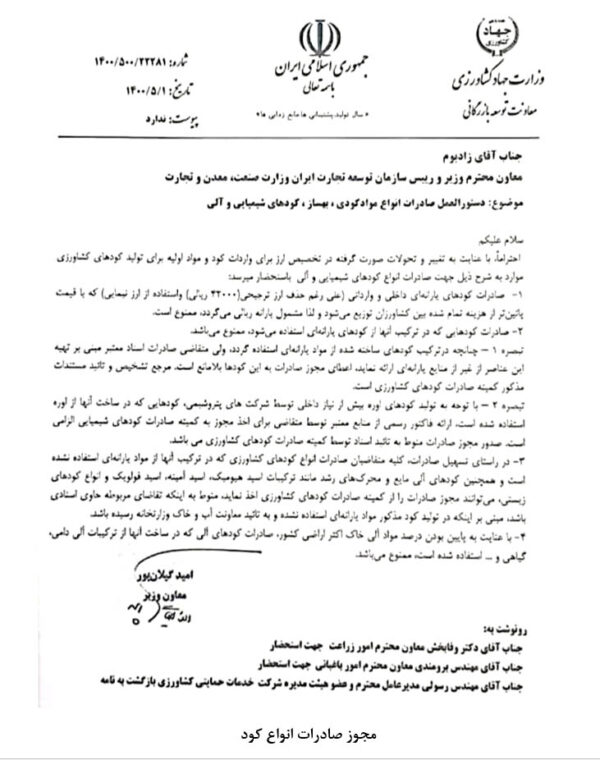
در حوزه بینالمللی پیشبینی میشود سه منطقه جنوب شرقی آسیا، چین، آمریکای مرکزی و جنوبی حدود 46 درصد کل مصرف کودهای نیتروژندار از جمله سولفات آمونیوم جهان را تشکیل خواهند داد.
پیشبینی موسسات معتبر بینالمللی نشان میدهد که اندازه بازار سولفات آمونیوم در دنیا تا سال 2027 به حدود 4 میلیارد دلار برسد.
در حال حاضر بیش از 75 درصد بازار سولفات آمونیوم در حوزه کود کشاورزی است که پیشبینیها نشان میدهد در سالهای آینده سایر بازارهای مصرف این محصول مانند صنایع غذایی، چوب و کاغذ، نساجی، دارویی و … افزایش خواهد یافت.
از جمله مهمترین تولیدکنندگان سولفات آمونیوم دنیا میتوان به چین، بلژیک، هلند، کره جنوبی و آمریکا اشاره کرد. چین بزرگترین صادرکننده سولفات آمونیوم دنیا بوده و نزدیک به 50 درصد صادرات این محصول در دنیا مربوط به چین است (حدود 7 میلیون تن).
در میان سایر کشورهای دنیا برزیل، اندونزی، ویتنام و ایالات متحده آمریکا و مالزی بزرگترین واردکنندگان سولفات آمونیوم هستند از که از مجموع 13 میلیون تن واردات سولفات آمونیوم در دنیا، 50 درصد واردات به این کشورها تعلق دارد.
کل تولید سولفات آمونیوم در دنیا بر اساس آخرین آمار سال 2021 حدود 30 میلیون تن است.
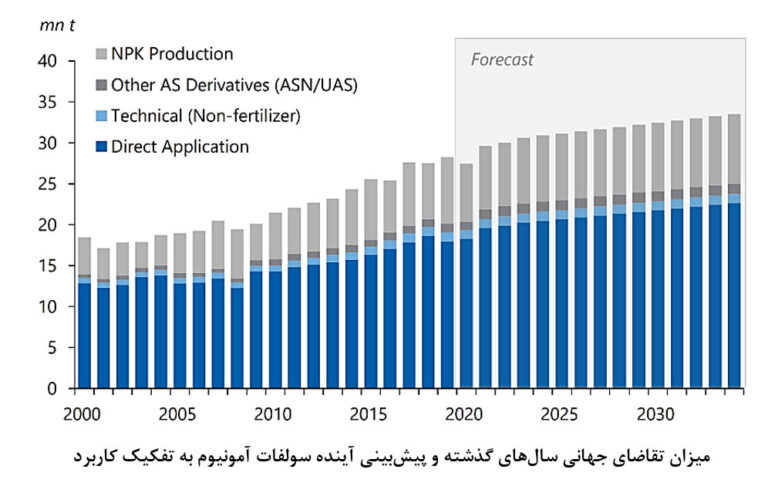
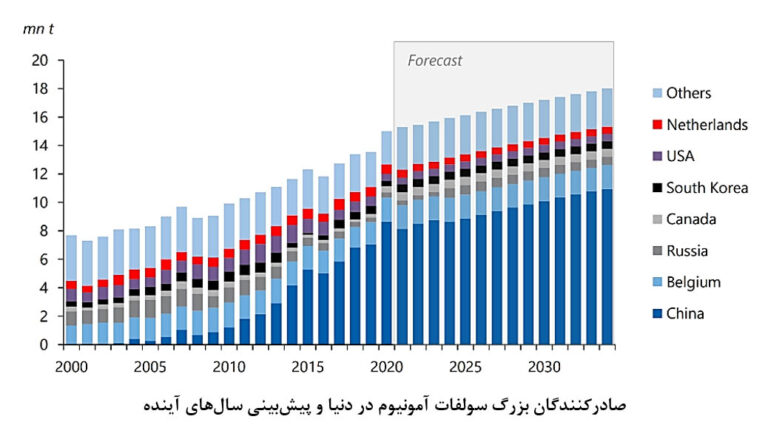
در حوزه داخلی، بر اساس آمار رسمی میزان مصرف ظاهری سولفات آمونیوم در کشور در بازه 120 تا 150 هزار تن متغیر بوده است.
پیشبینی عرضه و تقاضای کود سولفات آمونیوم برای سالهای آینده را میتوان در دو بعد مصرف داخلی و بازارهای صادراتی بررسی کرد:
الف) در حوزه مصرف داخلی با در نظر گرفتن حدود 8 میلیون هکتار زمین کشاورزی آبی و بر اساس این فرض که در هر هکتار زمین کشاورزی در شرایط ایدهآل به طور متوسط 150 کیلوگرم در هر سال کود سولفات آمونیوم مصرف شود، حداکثر ظرفیت مصرف کود سولفات آمونیوم در زمینهای کشاورزی باغی و زراعی (آبی) کشور 2/1 میلیون تن است.
مصرف ظاهری سولفات آمونیوم در کشور نشان میدهد در حال حاضر، تنها 10 درصد از زمینهای کشاورزی آبی ایران از این کود استفاده میکنند.
با فرض اینکه از سال 1401 سالیانه 10 درصد به مصرف سولفات آمونیوم کشور در زمینهای کشاورزی آبی افزوده شود، میزان مصرف این کود در سال 1405 به حدود 180 هزار تن در سال خواهد رسید.
بنابراین در تحلیل بازار داخلی نباید ظرفیت مصرف داخلی این کود را در 5 سال آینده بیش از 180 هزار تن در سال برآورد کرد.
شایان ذکر است عوامل مختلفی چون تغییر سیاست کلان کشور در اعطای یارانه کود اوره به کشاورزی، تاثیر مستقیم بر میزان استفاده از کود سولفات آمونیوم خواهد داشت (که این مساله در نظر گرفته نشده است)
ب) در حوزه بازارهای صادراتی: مهمترین بازارهای صادراتی برای سولفات آمونیوم ایران ترکیه و کشورهای جنوب شرق آسیا (مالزی، اندونزی و ویتنام)، عراق و سوریه هستند. در سالهای گذشته میزان واردات سولفات آمونیوم ترکیه بیش از 900 هزار تن در سال بوده است که در سال 2020 این میزان کاهش یافته و به حدود 400 هزار تن رسیده است.
اما کشورهای مالزی، اندونزی و ویتنام در مجموع حدود 3 میلیون تن واردات سولفات آمونیوم در سال 2020 را تجربه کردهاند.
با توجه به نقش مهم چین در تامین سولفات آمونیوم مورد نیاز کشورهای جنوب شرق آسیا، بازار عمده برای سولفات آمونیوم ایران بازار صادراتی ترکیه، عراق، سوریه و … خواهد بود.
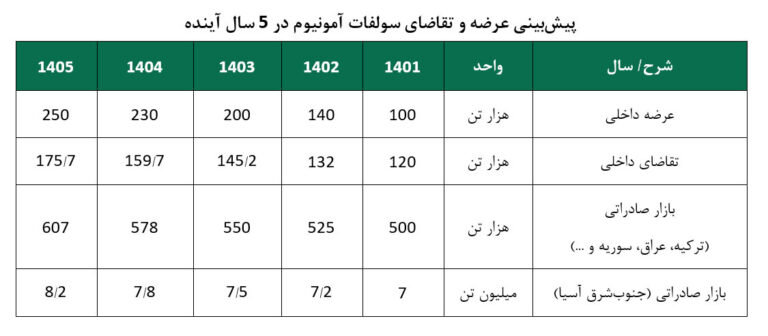
فناوری و روش تولید سولفات آمونیوم
حدود 90 درصد سولفات آمونیوم با سه روش اصلی تولید میشود (1) به عنوان محصول جانبی تولید کاپرولاکتام ([(CH2)5COHN]) (2) روش سنتزی و (3) محصول جانبی تولید گاز یا کک از زغالسنگ.
در برخی موارد سولفات آمونیوم، محصول جانبی تولید نیکل یا متیل متاکریلات نیز است.
سولفات آمونیوم به عنوان محصول جانبی فرایند اکسیداسیون کاپرولاکتام بدست میآید.
آمونیوم سولفات سنتزی نیز از طریق ترکیب شدن آمونیاک و اسید سولفوریک در یک راکتور تولید میشود.
همچنین آمونیوم سولفات به عنوان محصول جانبی تولید گاز یا کک از طریق واکنش میان آمونیاک بازیابی شده از گازهای خروجی فرایند تولید کک با سولفوریک اسید تولید میشود.
شکل 3 شمایی از فرایندهای مختلف تولید سولفات آمونیوم را به روشهای مختلف نشان میدهد.
بعد از تشکیل محلول سولفات آمونیوم، روش تولید تقریبا در همهی فرایندها مشابه یکدیگر است.
کریستالهای آمونیوم سولفات از طریق چرخاندن محلول آمونیوم سولفات در یک تبخیرکنندهی آب تولید میشوند.
در این فرایند محلول تغلیظ میشود. کریستالهای آمونیوم سولفات با فرایند سانتریفیوژ از محلول جدا میشوند.
در حالتی که آمونیوم سولفات به عنوان محصول جانبی فرایند تولید کاپرولاکتام است، محصول ابتدا به داخل یک تانک تهنشینی منتقل میشود تا میزان فاز مایع در فرایند سانتریفیوژ کاهش یابد و محلول اشباع شده در فرایند بازگردانده میشود.
کریستالها که پس از فرایند سانتریفیوژ حاوی 1 تا 5/2 درصد وزنی رطوبت هستند، به داخل یک بستر سیال یا خشککن گردان وارد میشوند.
در حالتی که سولفات آمونیوم به عنوان محصول جانبی تولید گاز یا کک است، از فیلترهای گردان خلا به جای سانتریفیوژ و خشک کن استفاده میشود. یک لایه محصول کریستالی بر روی فیلتر باقی میماند و به عنوان محصول از روی آن برداشته میشود.
کریستالهای تولید شده معمولا دارای توزیع وسیعی از اندازه ذرات هستند. گازهای خروجی فرایند از یک اسکرابرِ تر عبور میکند.
این فرایند موجب کنترل خروجی فرایند و بازیابی پسماندها میشود.
سولفات آمونیوم کریستالی بعد از خشک شدن دانهبندی شده و محصول نهایی تولید میشود.
ذرات ریز سولفات آمونیوم یکی از مهمترین موادی هستند که در طول فرایند ممکن است وارد محیط شوند.
مرحله خشک کردن بیشترین میزان ذرات ریز سولفات آمونیوم را تولید میکند که ممکن است وارد هوا شوند.
میزان ورود ذرات ریز به هوا به سرعت جریان گازهای داغ و توزیع اندازه ذره محصول بستگی دارد.
بسته به نوع خشک کن مورد استفاده در فرایند، سرعت جریان گاز داغ متفاوت خواهد بود. عموما، سرعت جریان گاز داغ در خشککنهای بستر سیال از خشککنهای گردان بالاتر است.
بنابراین نرخ ورود ذرات ریز به هوا در فرایندهای با خشککن بستر سیال بالاتر است.
در برخی واحدهای صنعتی از فیلترهای کیسهای برای کنترل ورود ذرات ریز به هوا استفاده میشود اما در عین حال اسکرابرهای تر مانند ونتوری و اسکرابرهای سانتریفیوژی عملکرد بهتری دارند.
در اسکرابرهای تر ذرات جامد گرفته شده در این مرحله میتوانند مجددا به فرایند برگردانده شوند.
روشهای مختلفی برای تولید سولفات آمونیوم مورد استفاده قرار میگیرد.
انتخاب روش تولید عموما با توجه به مواد اولیه در دسترس انجام میشود.
عمده روشهای تولید سولفات آمونیوم عبارتاند از:
- واکنش میان آمونیاک و اسید سولفوریک در یک محفظه تبخیری اشباع در شرایط خلا یا فشار اتمسفری و جدا کردن کریستالهای تولید شده به روش سانتریفیوژ یا فیلتراسیون.
- استفاده از آمونیاک آزاد شده در فرایندهای تولید کک و واکنش دادن آن با اسید سولفوریک و جدا کردن کریستالهای تولید شده به روش سانتریفیوژ یا فیلتراسیون.
- واکنش دادن کربنات آمونیوم با سولفات کلسیم، جدا کردن کربنات کلسیم به روش فیلتراسیون، تبخیر و کریستالیزاسیون سولفات آمونیوم از محلول به روش سانتریفیوژ.
- تبخیر کردن محصولات جانبی مایع حاوی سولفات آمونیوم و جدا کردن ماده جامد تولید شده به روشهای: کریستالیزاسیون و سانتریفیوژ، گرانولسازی و خشک کردن.
- واکنش مستقیم آمونیاک گازی با اسید سولفوریک در راکتور برای تولید محصولات آمورف و خشک.
- تولید همزمان سولفات آمونیوم و سایر نمکهای آمونیوم در فرایند گرانولسازی برای تولید کودهای فسفاته، نیتراته و نیتروفسفاتهی حاوی سولفات آمونیوم.
- سایر روشهای متفرقه مانند بازیابی سولفات آمونیوم از SO2 از گاز در حال جریان و یا بخار سولفوریک اسید.
روش کریستالیزاسیون:
کریستالیزاسیون یکی از روشهای عمده برای تولید سولفات آمونیوم و سایر نمکهاست.
دو موضوع عمده در فناوری کریستالیزاسیون وجود دارد.
اولین موضوع، تشکیل جوانه در محلول فوق اشباع و دوم، رشد این جوانهها تا رسیدن به اندازه مورد نظر برای محصول نهایی است.
در هر دو مرحله فوق، نیروی محرکه ایجاد شده از طریق میزان فوق اشباع محلول اصلی است.
اگر میزان فوق اشباع محلول مادر بیش از اندازه باشد، موجب جوانهزنی غیرقابل کنترل خواهد شد.
کنترل مرحله دوم از مرحله اول آسانتر است و میتوان با تغییر پارامترهای فرایند رشد جوانهها را کنترل کرد.
زمانی که یک محلول به سرعت تا محدودهی مشخصی سرد میشود، جوانههای جامد در آن پدیدار میشوند و یک حالت نیمه پایدار را ایجاد میکند.
بعد از رسوبدهی اولیه، این محلول ناپایدار است و اضافه کردن پایدار یک محلول نیمه پایدار موجب خواهد شد تا جوانههای جامد بوجود آمده به صورت تک کریستال رشد کنند.
بنابراین کنترل شرایط نیمه پایدار ذکر شده یکی از مهمترین بخشهای کنترلی در فرایندهای کریستالیزاسیون در واحدهای صنعتی است.
پارامترهایی مانند زمان ماند، همزدن، pH، دما و ناخالصیهای محلول و نامحلول موجود در سیستم از جمله پارامترهای مهم در کنترل فرایند محسوب میشوند.
برای انجام یک فرایند پایدار و پیوسته لازم است تا تعادلی میان تعداد جوانههای جامد ایجاد شده و کریستالهای در حال رشد برقرار شود.
در این شرایط کریستالهای با اندازه یکنواخت تولید میشوند.
در این حالت با یک شارژ پیوسته و ثابت امکان تولید محصولی با توزیع اندازه دانه یکنواخت وجود دارد.
کنترل پارامترهای ذکر شده در کریستالایزرهای مدرن از طریق سیستمهای کنترلی به صورت خودکار انجام میشود و محصول تولید شده با توزیع اندازه ذرات معین با شارژ پیوسته مواد اولیه مورد انتظار است.
تناژهای بالایی از سولفات آمونیوم از آمونیاک و اسید سولفوریک در کریستالایزرهای پیوسته تحت شرایط خلا یا در فشار اتمسفر تولید میشود.
در حالتی که واکنش در شرایط خلا انجام میشود، حرارت واکنش از طریق تبخیر آب همراه اسید و یا آبی که برای کنترل دما به سیستم اضافه میشود، کاهش مییابد.
این روش برای حالتی که فرایند در فشار اتمسفری انجام میشود نیز استفاده میگردد.
روش دیگر برای کاهش حرارت، دمیدن حجم بالایی هوای خنک به درون دوغاب ایجاد شده است.
واکنش میان گازها، امونیاک و سولفوریک اسید به صورت زیر انجام میشود:

در عمل میزان حرارت ایجاد شده توسط واکنش حدود 2350 کیلوکالری به ازای هر کیلوگرم نیتروژن است.
پس از انجام واکنش و بوجود آمدن محصول با توزیع اندازه ذرات مشخص، جدا کردن ذرات از محلول از طریق سانتریفیوژ انجام میشود.
شست و شو با آب یا محلول آمونیاک انجام شده و عملیات خشک کردن در خشککنهای گردان اتفاق میافتد.
در نهایت محصول خشک شده غربال و سرند شده و بستهبندی میشود. در برخی واحدهای صنعتی، تولید ذرات با اندازه درشت و خوب شسته شده به همراه استفاده از سانتریفیوژهای با بهرهوری بالا، نیاز به مرحله خشک کردن را از بین میبرد.
در صورتی که ذرات با اندازه ریز و همراه با برخی ناخالصیها تولید شوند، مرحله شست و شو و خشک کردن و به دنبال آن خنک کردن غیر قابل اجتناب است.
در مرحله سرند کردن، ذرات ریز از ذرات درشت جدا میشوند و ذرات ریز مجددا به داخل کریستالایزر برمیگردند.
روش دیگر برای بازیابی کریستالها و تحت عملیات قرار دادن آن، استفاده از یک فیلتر – خشک کن تحت خلا است.
همچنین از روش گرانولسازی کریستالهای ریز توسط یک گرانولاتور نیز میتوان بهره برد.
سولفات آمونیومی که به عنوان کود مورد استفاده قرار میگیرد، باید دارای حداقل 5/20 درصد وزنی نیتروژن باشد.
همچنین میزان اسید و رطوبت آزاد آن باید حداقل 2/0 درصد وزنی باشد.
توزیع اندازه ذرات محصول نیز بسته به نیاز مشتری و نوع کاربرد متغیر است.
برای استفاده مستقیم یا مخلوط کردن به صورت بالک، کریستالهای بزرگ با اندازه 1 تا 3 میلیمتر مورد نیاز است.
برای تعیین اندازه ذرات محصول تغییر و بهینه کردن پارامترهای تولید لازم است و در برخی موارد از افزودنیهایی برای کنترل محدوده اندازه ذرات نیز استفاده میشود.
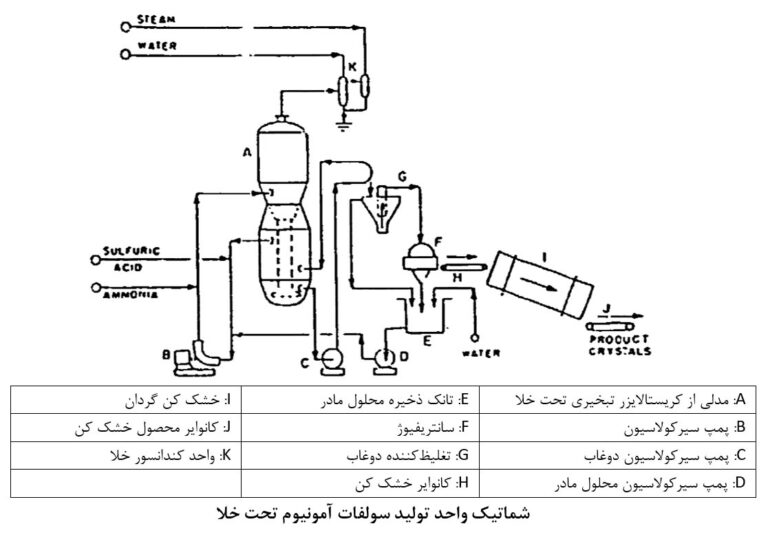
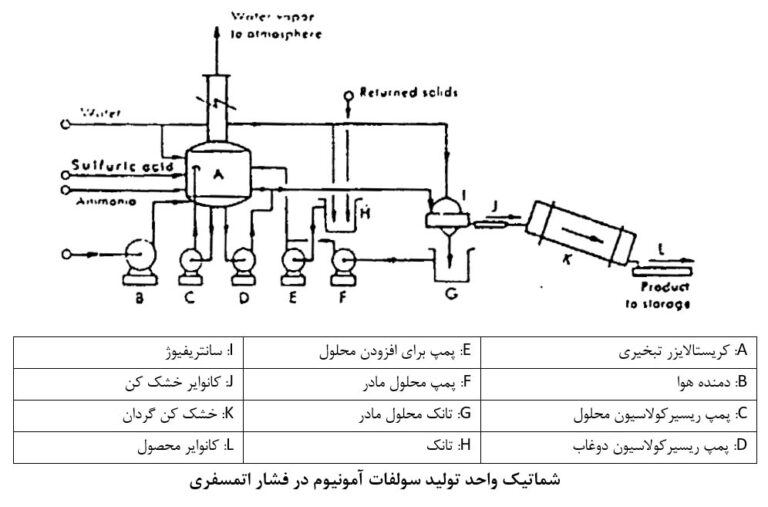
محلول سولفات آمونیوم بسیار خورنده است و در طراحی و ساخت تجهیزات باید مورد توجه قرار گیرد و از تجهیزاتی از جنس فولاد زنگ نزن یا فولاد ساختمانی روکش شده با لاستیک استفاده شود.
روش تولید سولفات آمونیوم به عنوان محصول جانبی فرایندهای گازی:
قبل از در دسترس و فراوان بودن سولفات آمونیوم سنتزی در دهه 1920، عمده آمونیاک مصرفی در دنیا از طریق واحدهای کربونیزاسیون تامین میشد.
زغالسنگهای بیتومینی مورد استفاده برای تولید گاز یا کک، حدود 1 تا 2 درصد وزنی نیتروژن دارند و 15 تا 20 درصد این میزان میتواند به صورت آمونیاک بازیابی شود به طوری که به ازای هر تن زغالسنگ مورد استفاده در فرایند، 5/2 تا 3 کیلوگرم آمونیاک تولید شود.
زدایش آمونیاک از گاز به دو دلیل جلوگیری از خوردگی و همچنین تولید یک محصول جانبی با صرفه اقتصادی قابل قبول انجام میشود.
سه روش عمده برای بازیابی آمونیاک یا نمکهای آن به عنوان محصول جانبی فرایندهای تولید کک یا گاز وجود دارد.
روش مستقیم، غیرمستقیم و نیمه مستقیم.
در روش نخست (مستقیم)، گاز حاصل از فرایند خنک شده تا تا حد ممکن قیر آن زدوده شود و سپس از داخل یک اشباع ساز یا اسکرابر عبور کرده و با اسید سولفوریک شست و شو داده میشود.
دوغاب سولفات آمونیوم تولید شده، تحت عملیات سانتریفیوژ قرار گرفته، شست و شو شده و خشک میشود و محصول مورد نظر بسته بندی و ذخیرهسازی میگردد.
از مزایای این روش میتوان به نرخ بازیابی بالا، حجم سرمایهگذاری پایین در تجهیزات و ماشینآلات، هزینههای تولید پایین و میزان پساب تولیدی پایین اشاره کرد.
در بسیاری از موارد، محصول تولیدی به این روش، ناخالصیهایی دارد که باید قبل از فروش رکریستالیزه شود.
همچنین وجود یونهای کلر در محلول موجب انجام واکنش و تولید کلرید آمونیوم شده که باعث خوردگی تجهیزات، لولهها و اتصالات میشود که باید با استفاده از مواد مناسب و همچنین پوششدهی از خوردگی تجهیزات جلوگیری کرد.
برخی مشکلات مربوط به روش مستقیم موجب ابداع روش غیرمستقیم تولید سولفات آمونیوم شد.
در این روش گاز تولیدی در فرایند ابتدا به کمک تماس با محلولهای فرایند و یا آب سیرکوله، خنک شده و محلولها به قسمت بالایی برج تقطیر آمونیاک پمپ میشوند که با تماس با بخار آمونیاک آزاد میکند.
سپس در اثر تماس با آهک، برخی نمکهای آمونیوم مانند آمونیوم کلرید تجزیه شده و بخار خارج شده از قسمت بالایی برج گاز امونیاک خالص است که در نهایت با اسید سولفوریک مورد شست و شو قرار گرفته و سولفات آمونیوم تولید میکند.
یکی از مهمترین مزایای این روش، تولید محصول با میزان ناخالصیهای پایین و انعطافپذیر بودن برای تولید انواع محصولات و مشتقات آمونیاک است.
اما در عین حال دارای هزینههای عملیاتی بالا بوده و نحوه دفع پسماندهای حاصل از فرایند پیچیده است.
روش نیمه مستقیم، تلفیقی از روش مستقیم و غیرمستقیم است به طوری که گاز در ابتدا خنک شده و مورد شست و شو قرار میگیرد تا قیر و سایر رسوبات آن زدوده شود.
محصول این مرحله در یک برج تقطیر نسبتا کوچک آمونیاک وارد میشود و آمونیاک آزاد شده با جریان اصلی بخار ترکیب میشود و تا دمای 70 درجه سانتیگراد حرارت دیده و توسط محلول حاوی سولفات آمونیوم اشباع و 5 تا 6 درصد سولفوریک اسید شست و شو داده میشود که این عمل در یک اسکرابر انجام میشود.
فرایند آمونیوم کربنات و کلسیم سولفات (گچ)
این روش در آلمان آغاز شده و در کشورهایی مانند اتریش، هند، پاکستان و انگلیس توسعه یافته است.
این روش بر مبنای ترکیب کردن آمونیاک و دیاکسید کربن با هدف تولید آمونیوم کربنات است که پس از تولید یا کلسیم سولفات (گچ) واکنش داده و سولفات امونیوم و کربنات کلسیم تولید میکند.
بازیابی سولفات آمونیوم از محصول جانبی فرایندهای تولید کاپرولاکتام و اکریلونیتریل
در این روش از بخار خارج شده از فرایند تولید کاپرولاکتام یا اکریلونیتریل برای تولید سولفات آمونیوم استفاده میشود.
برج اسپری
یکی دیگر از روشهای تولید سولفات آمونیوم استفاده از برج اسپری است.
در این روش اسید سولفوریک در داخل برج حاوی بخار آمونیاک اسپری میشود و حرارت ایجاد شده در اثر واکنش، موجب تولید یک محصول خشک و آمورف با توزیع اندازه دانه کمتر از 300 مش میشود.
محصول تولید شده به طور پیوسته از قسمت پایینی برج توسط یک اسکرو کانوایر خارج میشود. محصول تولیدی به این روش گرانوله شده و مورد استفاده قرار میگیرد.
روش پیشنهادی ساینوتک:
برای تولید سولفات آمونیوم گرانول از تکنولوژی پایپ راکتور – گرانولاتور و برای تولید سولفات آمونیوم کریستالی از تکنولوژي کریستالایزر اسلو (Oslo Crystallizer) استفاده میشود.
در روش پایپ راکتور – گرانولاتور، آمونیاک مایع و اسید سولفوریک در مخازن مخصوص ذخیره میشوند و به نسبتهای مشخص از طریق سیستم پایپینگ و پمپهای تعبیه شده در خط به همراه محلول سولفات آمونیوم در گردش فرآیند، وارد راکتور لولهای (Pipe Reactor) میشوند.
طول لوله واکنش بین 15 – 10 متر است و بخشی از واکنش اصلی میان اسید سولفوریک و آمونیاک برای تشکیل سولفات آمونیوم در این راکتور انجام میشود.
دوغاب تولید شده در این راکتور وارد دستگاه گرانولاتور واکنشی (Granulator) شده و در این مرحله نسبت مشخصی آمونیاک و آب برای تکمیل واکنش و کنترل شرایط محصول افزوده میشود.
گرانولهای تولید شده در این مرحله در یک یا چند نوبت وارد کولر دوار (Rotary Cooler) شده و پس از خنک شدن از طریق یک باکت الواتور (یا نوار نقاله) به سرند منتقل میشوند.
ذرات درشت و ریز در سرند جدا شده و ذرات درشت وارد آسیاب میشوند.
ذرات در اندازه مطلوب 6 – 3 میلیمتر به عنوان محصول گرانول وارد واحد بستهبندی شده و بخشی از ذرات ریز مجددا توسط نوار نقاله به گرانولاتور برگردانده میشوند تا بستر واکنش آماده باشد.
در این فرایند از سیستمهای ونتوری – اسکرابر استفاده میشود. اسکرابر گازهای خروجی به همراه ذرات معلق را از گرانولاتور به کمک یک مکنده دریافت میکند.
همچنین غبارهای تولید شده در فرایند خنک کاری در کولر دوار نیز مکش شده و در نهایت در فرایند بازیابی میشوند و از ورود آن به محیطزیست و همچنین اتلاف محصول جلوگیری میشود.
با اضافه کردن یک سیستم محلولساز و کریستالایزر به خط تولید امکان تولید سولفات آمونیوم کریستال نیز وجود دارد.
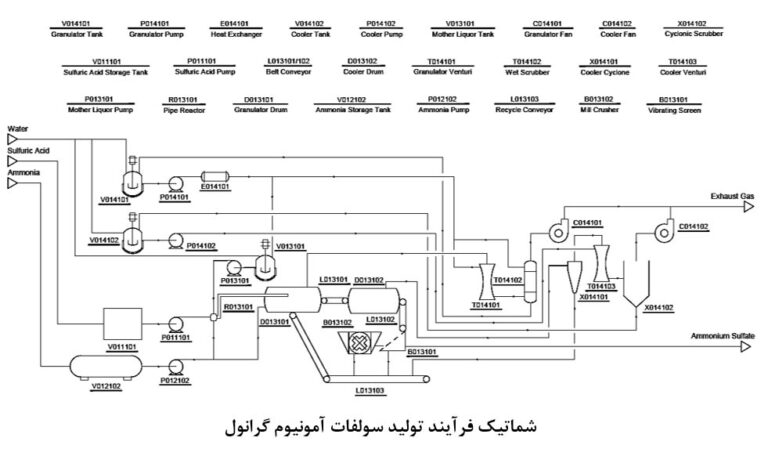
مسائل و چالش های زیست محیطی
براساس استاندارد ملی ایران به شماره 22315، صنایع شیمیایی و واحدهای تولید انواع کودهای شیمیایی مشمول نصب سامانههای پایش لحظهای و برخط بر روی آلایندههای محیطزیست هستند.
واحدهای تولید انواع کودهای شیمیایی در گروه فیزیکی و شیمیایی باید پارامترهای TSS/Turbidity، pH، EC، BOD، COD، دما، آمونیاک، فسفات و نیترات و فلو و در گروه هوا، ذرات، SO2، CO، Flow rate، O2، NH3 و NOX را تحت پایش قرار دهند.
حد مجاز آلایندهها مطابق با جدول زیر است.
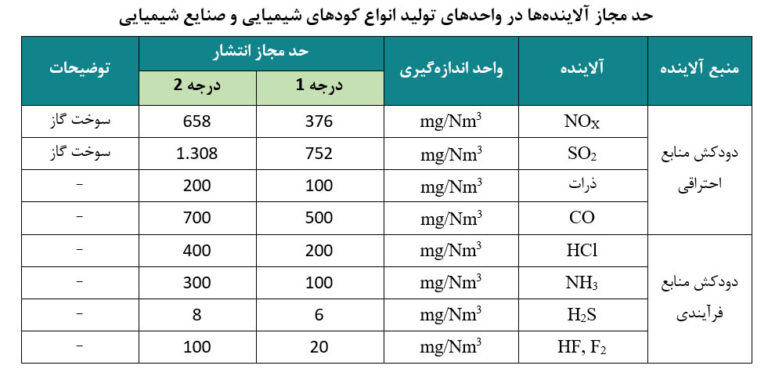
سه نوع پسماند اصلی در واحدهای تولید مواد شیمیایی و کودهای کشاورزی مورد نظر است.
با توجه به شباهت اصول طراحی فرآیندهای تولید انواع مواد شیمیایی و کودهای کشاورزی، کنترل آلایندهها از طریق سه روش کلی انجام میشود:
- کنترل گرد و غبار متصاعد شده در اثر جابجایی و انتقال مواد و جریان مواد جامد در خط تولید از طریق سیستمهای ونتوری – اسکرابر، سیکلون – ونتوری – اسکرابر و سیکلون – بگ فیلتر به منظور قرار گرفتن میزان آلایندههای منتشر شده در خطوط تولید در حد مجاز ذکر شده در جدول شماره 13
- دپوی محصولات جانبی جامد و مایع تولید شده در فرآیندها به صورت ذخیره در مخازن و یا دپو در محلهای استاندارد که ذخیره یا دپوی آنها میتواند با هدف فروش محصول، استفاده در سایر واحدها و فرآیندها و یا دپو به عنوان پسماند غیرقابل استفاده اما بدون آثار سوء زیستمحیطی باشد.
- بازچرخانی (سیرکولاسیون) مواد در داخل فرآیند از طریق جذب گازهای متصاعد شده در طول فرآیند بوسیلهی ستونهای جذب، سیستمهای اسکرابینگ و ونتوری – اسکرابرها و ذخیره آنها در مخازن یا حوضچهها به منظور بازچرخانی و استفاده مجدد در فرآیند.
بنابراین عمده تجهیزات مورد استفاده برای جلوگیری از ورود بیش از حد مجاز آلایندهها به محیطزیست شامل موارد زیر است که این تجهیزات میتوانند به تنهایی و یا به صورت ترکیبی برای کنترل آلایندهها مورد استفاده قرار گیرند:
- سیکلونها (Cyclones)
- بگ فیلترها (Bag Filters)
- ونتوریها (Venturies)
- سیستمهای اسکرابینگ و برجهای جذب (Wet scrubbers & adsorption towers)
- مخازن ذخیره (Residual storage tanks)
- حوضچههای ذخیره (Residual storage ponds)
- ایجاد محلهای مناسب و استاندارد دپوی مواد (مانند: سد باطله – Waste dam)
شایان ذکر است در واحد صنعتی از سیستمهای کنترل و مانیتورینگ آنلاین آلایندهها استفاده شده است.
در صورتی که سیستمهای مانیتورینگ افزایش میزان آلایندهها را از حد مجاز نشان دهند (Bad Operation)، پارامترهای فرآیندی به منظور جلوگیری از ورود آلایندهها به محیطزیست اصلاح میشود و در صورت تداوم این امر، خط تولید برای بهینهسازی و اصلاح فرآیندها متوقف میشود.
انواع پسماندهای خط تولید سولفات آمونیوم به شرح زیر است:
- پسماندهای جامد: گرد و غبار کود سولفات آمونیوم
- پسماندهای گازی: گاز آمونیاک
- پسماندهای مایع: محلول سولفات آمونیوم
طراحی فرآیند تولید سولفات آمونیوم گرانول و کریستال به نحوی انجام میشود که هیچ پسماند گاز، جامد و مایعی خارج از حد مجازها و استانداردها از کارخانه خارج نشود.
بدین صورت که گازهای آمونیاک و بخارات موجود در محفظه درام گرانولاتور و کولر از طریق سیستم ونتوری – اسکرابینگ جذب شده و مجددا در آب فرآیندی در گردش حل میشوند و به خط تولید سیرکوله میشود.
همچنین در محل ریزش مواد در کلیه تجهیزات انتقال مواد، هود به همراه سیستم داکتینگ و فن نصب شده و غبارات احتمالی تولید شده در اثر حرکت مواد در خط تولید جمعآوری و توسط سیکلون مجددا به فرآیند سیرکوله میشوند.
بنابراین تنها محدودیت زیستمحیطی، مانیتورینگ میزان گاز آمونیاک خروجی از دودکشهای تعبیه شده است که با نصب یک دستگاه آنالایزر گاز آمونیاک امکان پایش مستمر آن وجود دارد.
در شرایط خاص و در صورت افزایش میزان ورود آمونیاک به محیطزیست در اثر Bad Operation، با تنظیم پارامترهای فرآیندی توسط سیستم اتوماسیون صنعتی تعبیه شده مانند:
دور چرخش گرانولاتور، میزان مکش فن، میزان اسپری آب در داخل گرانولاتور، تنظیم دبی مول دوم آمونیاک، تنظیم pH مخزن آب فرآیندی و … جذب آمونیاک در سیستم اسکرابینگ تنظیم شده و گاز خروجی از دودکش به بازه حد مجاز تعریف شده میرسد.
شکل زیر شماتیک پسماندهای خط تولید سولفات آمونیوم را نشان میدهد.
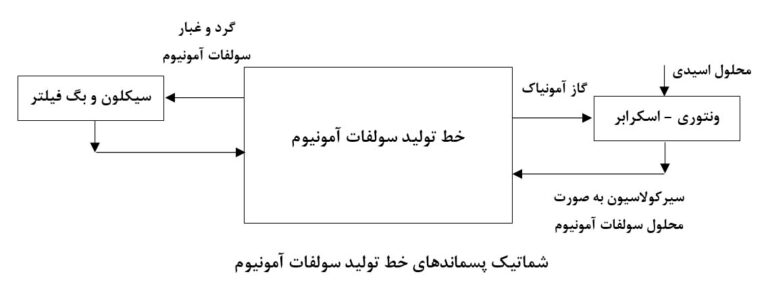
به منظور جلوگیری از نشت هرگونه محلول اسیدی یا محلول سولفات آمونیوم به محیطزیست، از مخازن پلی پروپیلنی (PP) و یا حوضچههای بتنی دارای پوشش ژئوممبران استفاده میشود.
بنابراین انتشار کلیه آلایندههای احتمالی خط تولید سولفات آمونیوم مطابق با حد مجازها و استانداردهای زیستمحیطی بوده و هیچ پسماندی برای دپو و یا انتقال به خارج از کارخانه وجود ندارد.